Meeting Today’s Construction Challenges with Prefabrication
Tuesday May 6, 3:45pm-4:45pm
Centennial E-H
Prefabrication is believed by many to be the future of construction. It allows for more efficient use of the dwindling supply of skilled labor, tighter quality controls, and better conditions for assembly of complex building systems. BPL Enclosure and Mortenson will present a case study demonstrating how panelization and prefabrication of the building enclosure can meet the challenges of today’s construction environment. The presentation will discuss the two main types of prefabrication used in commercial construction today: modular and panelized construction. Review design and construction phase differences between conventional and panelized construction. Review the design and construction phase advantages and disadvantages of panelized construction. Present a case study of a Denver area building where the levels above the podium were constructed entirely of prefabricated wall and floor panels where the exterior wall panels were delivered to the site with the exterior cladding materials in place and fully glazed. The case study will focus on the building enclosure and present how disadvantages of panelized construction were overcome and unanticipated conditions addressed throughout the project. We will discuss the design of the heat, air, and moisture control elements as well as panel-to panel transitions. The case study will also present how the project was able to comply with local requirements pertaining to the building enclosure including Denver Energy Code Air Barrier Performance Verification requirements.
Learning Objectives:
- Identify the advantages and disadvantages of prefabrication as it compares to conventional construction.
- Identify the key building enclosure elements and how they can be detailed and designed for panelized construction.
- Apply potential strategies for overcoming construction challenges of prefabricated panelization using a completed Denver project to demonstrate how solutions were implemented throughout the project.
- Implement pathways for compliance with IECC 2021/Denver Energy Code 2022 air barrier performance verification requirements for prefabricated enclosure construction.
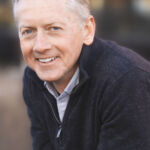
David Young, AIA, NCARB, LEED AP, BECxP, CxA+BE
BPL Enclosure, Denver CO
David started his professional career in Chicago working for a small firm that specialized in the evaluation and repair of existing buildings. The work consisted of mostly of high-rise façade repair but also included parking garage repair, waterproofing and roofing system replacement, water intrusion investigations, and testing. He gained considerable exposure to stone, terra cotta, and brick masonry; concrete; window and curtain wall; as well as roofing and waterproofing. In 2007, he moved to Denver and the focus of his practice shifted from existing buildings to new construction. His practice areas in Colorado have focused on building enclosure design peer review and consulting, building enclosure commissioning, building science, building enclosure condition assessment, testing, and construction phase quality.
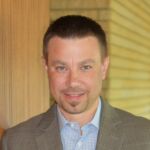
Robert Zdenek
Mortenson
Rob is the Enclosure Executive at Mortenson Construction. With over six years in this position at Mortenson Rob has facilitated the delivery of quality enclosures on projects of all types including Hospitality, Office, Healthcare, and Data Centers. Rob brings a wealth of knowledge and boots on the ground experience to the enclosure aspects of dozens of projects across the nation each year.